Effective Use of Defoamers in the Pharmaceutical Manufacturing Process
The Function of Defoamers in Enhancing Item High Quality and Performance
Defoamers serve as vital additives that alleviate this concern, ensuring smoother production process while boosting the functional and aesthetic features of the last items. The choice of the suitable defoamer can be important to attaining optimal results, raising essential concerns regarding solution compatibility and efficiency metrics that warrant more expedition.
Recognizing Defoamers
Understanding the role of defoamers is important for preserving product quality across various markets. Defoamers are chemical additives developed to avoid the formation and minimize of foam in fluid systems, which can adversely affect processes such as mixing, filling, and surface stress. Frothing can bring about inadequacies, item flaws, and jeopardized aesthetic appeal, making defoamers an important element in producing operations.
In commercial applications, defoamers aid to improve product consistency and security. In the paint and coverings industry, foam can conflict with the application process and the final coating. In a similar way, in food and beverage manufacturing, too much foam can impede bottling and product packaging effectiveness (defoamers). The efficient usage of defoamers not just guarantees smoother manufacturing processes but additionally adds to superior item performance.
In addition, the selection and solution of a defoamer should straighten with particular application requirements, such as compatibility with various other components, efficiency under differing temperature and pH conditions, and potential regulative restraints. Ultimately, recognizing defoamers' functions and their value in numerous formulas is critical for optimizing manufacturing and ensuring the best quality end products.
Kinds of Defoamers
Defoamers can be categorized right into numerous types based on their structure and device of activity. The primary types consist of silicone-based, non-silicone natural, and not natural defoamers.
Silicone-based defoamers are among the most efficient, largely because of their capacity to spread swiftly on the fluid surface and interrupt foam formation. Their one-of-a-kind chemical framework allows for remarkable security, making them ideal for high-temperature applications and environments with varying pH levels.
Non-silicone organic defoamers, commonly made up of all-natural oils or fats, are valued for their biodegradability and reduced poisoning. These are typically utilized in food and beverage applications where safety and environmental impact are critical.
Inorganic defoamers, which include compounds like talc or calcium carbonate, act by boosting the thickness of the fluid, therefore reducing foam stability. They are frequently made use of in commercial procedures where compatibility with various other products is not a worry.
Each kind of defoamer has distinct benefits and restrictions, enabling tailored solutions depending on the specific foaming concerns run into in numerous applications. Comprehending these differences is essential for optimizing efficiency and attaining preferred product top quality.
Applications Throughout Industries
Various industries utilize defoamers to boost product quality and functional effectiveness. In the food and beverage market, defoamers are important in processes such as developing and dairy products production to avoid foam development, which can bring about ineffectiveness and product incongruity. By managing foam, producers can ensure far better yield and an extra uniform product.
In the pharmaceutical sector, defoamers play a crucial role in the solution of liquid drugs, where excessive foam can restrain mixing and exact dosing. Their usage helps preserve the honesty of the formulas and facilitates smoother manufacturing procedures.
The paint and finishes industry likewise Web Site depends on defoamers to improve the efficiency of items during application. By lessening foam, these additives make sure a smoother finish and improve pop over here the visual qualities of the last product.
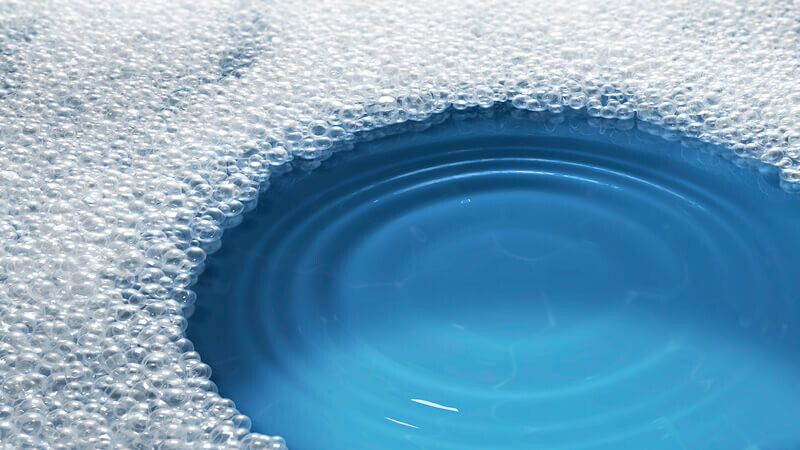
Advantages of Making Use Of Defoamers
While the application of defoamers differs throughout industries, their benefits regularly improve product quality and procedure performance. One substantial benefit is the decrease of foam formation during manufacturing procedures, which can or else cause production delays and inconsistencies in product top quality. By decreasing foam, defoamers make it possible for a smoother circulation of materials, helping with much more efficient procedures and minimizing the probability of devices malfunctions.
In addition, the use of defoamers can improve the look and structure of final items. In fields such as finishes, paints, and food processing, excessive foam can endanger the visual aesthetics and total high quality, while the suitable defoamer application ensures a consistent finish and preferable qualities. Defoamers can add to cost financial savings by reducing waste throughout production and optimizing the use of raw products.

Selecting the Right Defoamer
Selecting the right defoamer is essential for enhancing production processes and guaranteeing product quality. The choice of defoamer influences not only the performance of foam control yet additionally the total efficiency attributes of the final item. Elements to think about include the kind of application, the chemistry of the solution, and the ecological conditions under which the product will certainly be made use of.
Different industries might call for certain defoamer types, such as silicone-based, organic, or polymeric defoamers. Recognizing the compatibility of the defoamer with the main components is necessary to avoid adverse responses that might compromise item stability. Additionally, the defoamer's performance in different temperatures and pH degrees have to be examined to guarantee consistent efficiency.
Evaluating the defoamer in small applications can offer beneficial insights right into its performance and viability. Consideration of regulatory conformity, particularly in food, pharmaceuticals, and cosmetics, is extremely important in choosing a defoamer. Eventually, a complete evaluation of these elements will lead to the option of a defoamer that not only manages foam effectively however additionally enhances the high quality and efficiency of the final product.
Verdict
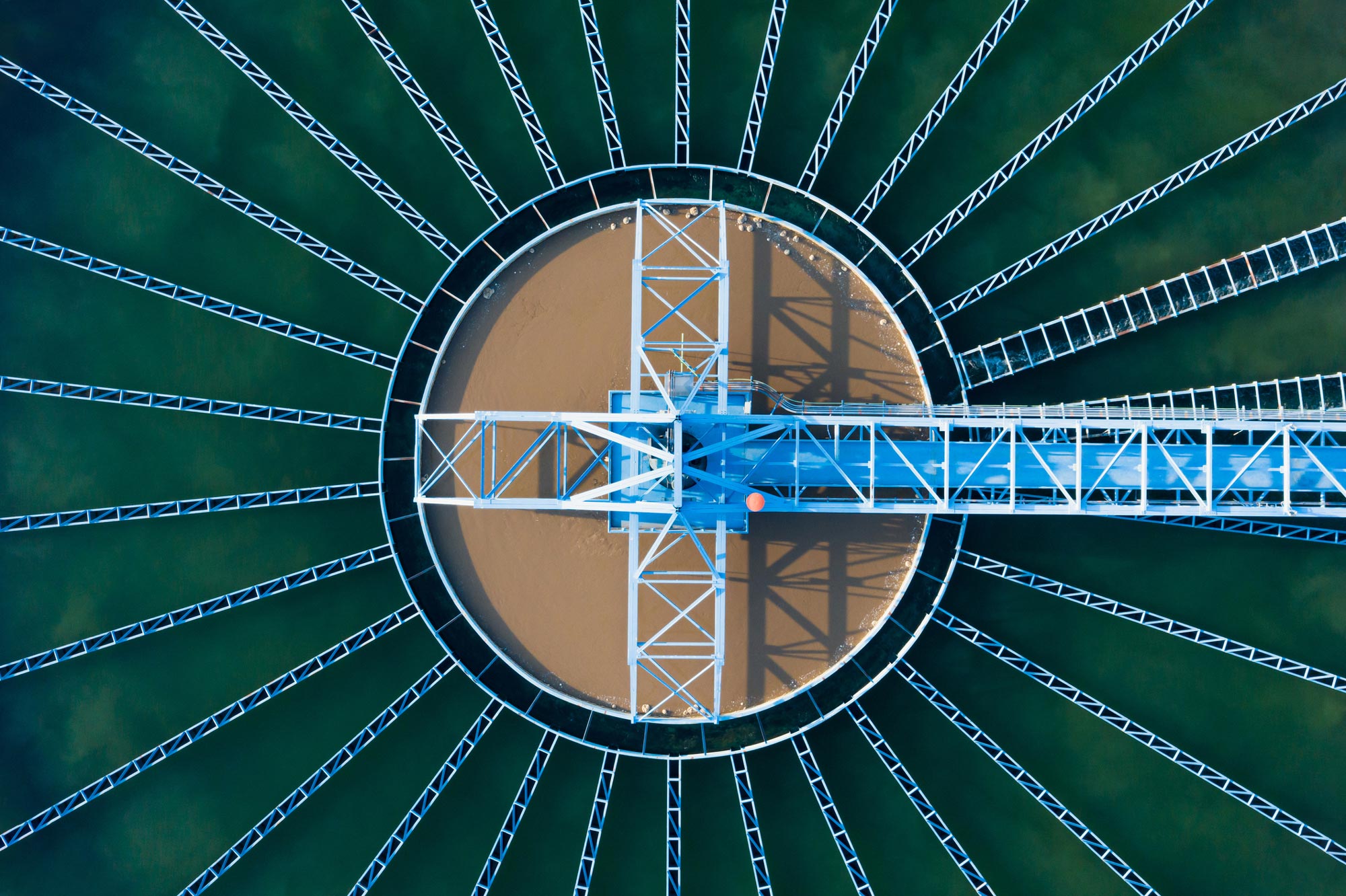
In conclusion, defoamers are important additives that dramatically boost item high quality and performance throughout numerous markets. The tactical hop over to here selection and application of defoamers lead to set you back financial savings, enhanced resource usage, and boosted client complete satisfaction.
Foaming can lead to inadequacies, product defects, and endangered visual appeal, making defoamers a crucial part in producing operations.
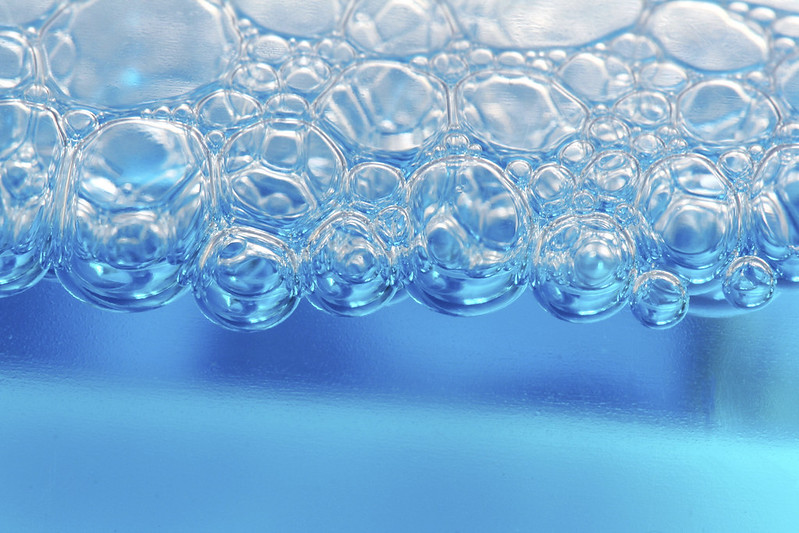